Hörende KI erkennt Qualitätsmängel bei Schweißprozessen in Echtzeit
Schweißroboter halten die Produktion zusammen. Im wahrsten Sinne des Wortes. Allerdings arbeiten sie nicht immer einwandfrei. Werden die meist feinen, aber unter Umständen bedeutenden Fehler erst spät entdeckt, waren alle weiteren Produktionsschritte umsonst und müssen mit einem neuen Ausgangsprodukt wiederholt werden. Das ist zeitaufwendig und teuer. Dank eines Systems aus Sensoren, die beim Schweißen zuhören und einer gut trainierten KI, die ihre Daten auswertet, lassen sich Mängel aber bereits an Ort und Stelle erkennen.
Vom Schiffsrumpf über seine gesamte Länge bis zu einem einzelnen Punkt, an dem zwei Bauteileteile aufeinandertreffen – fast überall dort, wo Metallteile präzise und robust miteinander verbunden werden, sind Schweißverfahren unverzichtbar. Allein für die Allure of the Seas, eines der derzeit bekanntesten Passagierschiffe, mussten Schweißnähte auf einer Länge von insgesamt 2,4 Kilometern gesetzt werden. Und das unter teilweise extremen Bedingungen: Grelles Licht, sprühende Funken und Temperaturen von mehreren Tausend Grad Celsius sind für die Fachleute ein erschwerendes, aber zwangsläufiges Übel. Schweißhelm, temperaturbeständige Handschuhe und Schutzkleidung erschweren das Hantieren mit Schweißgerät und Werkstück zusätzlich. In einem solchen Umfeld zu arbeiten ist kräftezehrend. Gleichzeitig erfordert das Schweißen exaktes handwerkliches Handling sowie höchste Konzentration.
Es ist deshalb kaum verwunderlich, dass die Industrie – wo immer es auch geht – das Schweißen so weit wie möglich zunehmend vollautomatisiert durchführt. Bei Metallteilen überschaubarer Größe ist eine von Automaten und Robotern präzise gesetzte Schweißnaht längst Standard. Zehntausendfach setzen die Schweißautomaten jeden Tag Tausende von Schweißpunkten. Jeder so exakt und präzise wie der erste. Oder sie ziehen über Stunden hinweg gleichmäßige Schweißnähte. Ohne Pause und ohne auch nur einmal kurz von der Ideallinie abzuweichen. Die Serienfertigung in der Automobilindustrie profitiert davon ebenso wie die Hersteller schwerer Stahlkonstruktionen im Schiffs- und Bahn- oder Kraftwerks- und Anlagenbau. Oftmals aber schweißen Automaten und Roboter die Metallteile nicht nur. Sie übernehmen mehr und mehr sogar die komplette Herstellung von Produkten: In additiver Fertigung bauen sie Schicht für Schicht Bauteile mit komplexen Geometrien auf. Ähnlich wie ein 3-D-Drucker, der Teile aus Kunststoff fertigt. Nur eben aus Stahl.
Automatisiert Schweißen hat nicht nur Vorteile
Einen Nachteil aber hat die automatisierte Vorgehensweise, und er ist gewichtig: Menschen können die Qualität ihrer Arbeit vor Ort weit besser beurteilen als Maschinen. Denn den Systemen fehlen die Fertigkeiten und die Fähigkeiten, mit Augen, Ohren und durch Fühlen die Qualität einer Schweißnaht zu beurteilen. »Erfahrene Arbeiter*innen hören meist schon am Geräusch, ob das Verschmelzen der Werkteile den kommenden Belastungen dauerhaft standhalten wird«, berichtet Kati Breitbarth vom Fraunhofer-Institut für Digitale Medientechnologie IDMT. Denn spezifische Laute, die unmittelbar während des Schweißvorgangs zu hören oder eben nicht zu hören sind, deuten auf Unregelmäßigkeiten im Prozess und damit auf mögliche Ausfälle in der Verbindung hin. Deshalb können erfahrende Schweißer*innen unmittelbar reagieren, um Geräte neu zu justieren, das eingesetzte Material zu überprüfen, nachzuarbeiten oder mangelhafte Teile zu entsorgen. Etwa wenn der Drahtvorschub stockt. Oder wenn der Verschleiß am Werkzeug so weit fortgeschritten ist, dass es ausgetauscht werden muss. Oder wenn Blasen innerhalb der Schweißnaht entstehen, die die Stabilität der Verbindung beeinträchtigen können.
Menschen sind besser
Bei dieser menschlichen Kontrolle vor Ort haben Schweißroboter und -automaten das Nachsehen. Sie arbeiten stupide weiter, auch wenn dabei Mängel entstehen. Mit anderen Worten: Erst bei der Nachkontrolle, meist am Ende eines Produktionsprozesses wird klar, dass nachgebessert werden muss. Und wenn auch das nicht möglich ist, muss der Betrieb mit teurem Ausschuss rechnen, denn er hat zusätzlich Zeit und Produktionskosten vergeudet.
Doch selbst eine nachgeschaltete Qualitätskontrolle der Schweißergebnisse ist aufwendig, betont Breitbarth: »Um Hohlräume im Inneren zu finden, müssen die geschweißten Teile Stück für Stück geröntgt werden. Oder es werden Stichproben gezogen, die für eine detaillierte Untersuchung sogar zerstört werden müssen.«
Vor allem im Bereich der additiven Fertigung mit Losgröße 1 sei der derzeitige Status quo ein regelrechter »Effizienzkiller«. Dank spezieller Schweißverfahren, wie dem Rührreibschweißen, ließen sich zwar Einzelteile für die Reparatur etwa von Schienenfahrzeugen oder Maschinen schnell herstellen. Doch mit der Herstellung allein sei es eben nicht getan. Die Teile müssen nun – wie alle anderen geschweißten Produkte auch – nachweislich auf Qualität und Sicherheit geprüft werden. Und dafür bleibe der Aufwand hoch.
Schweißroboter lernen Hören
Um das zu ändern, entwickeln Forscher*innen von Fraunhofer IDMT gemeinsam mit Partnern aus Wissenschaft und Industrie in einem vom Bundesministerium für Bildung und Forschung geförderten Projekt ein neuartiges Verfahren, das zur akustischen Kontrolle von Schweißnähten genutzt werden kann – und das in Echtzeit während des Fertigungsprozesses. »Ein Mikrofon als Ohr und eine KI zur Analyse – mehr wollen wir dafür eigentlich gar nicht einsetzen«, erklärt Breitbarth das Ziel des Projekts »AKoS«. Trotzdem aber, so Breitbarth, »wollen und müssen wir Schritt für Schritt vorgehen«.
Zunächst haben die Projektpartner deshalb einen Messkoffer mit speziellem Equipment entwickelt und erprobt. Darin enthalten sind neben einem Set an Mikrofonen, die unterschiedliche Frequenzen und Umgebungsbereiche erfassen können auch Vibrationssensoren, die direkt an dem Schweißautomaten angebracht werden sowie Datenschnittstellen, mit denen sich wichtige Parameter der Maschine auslesen lassen. »Mit die größte Herausforderung dabei war es, diejenigen Töne und Geräusche der Schweißgeräte aufzuzeichnen, in denen der Fügeprozess nicht reibungslos abläuft, sondern Mängel in der Ausführung auftreten«, betont Breitbarth. Denn natürlich sei die Akustik je nach Schweißvorgang, Material, dem Einsatz vor Ort sowie für jede Art von Prozessunregelmäßigkeit immer einer andere. Gemeinsam mit Schweißspezialisten entwickelte das Forschungsteam dazu einen Plan für erste Laborversuche: Sie manipulierten gezielt Werkzeuge und Materialeigenschaften, um Referenzgeräusche für fehlerhafte Schweißvorgänge aufzeichnen. Danach wurde das Prozedere zusätzlich noch bei Industriepartnern vor Ort in deren Schweißereien durchgeführt.
KI lernt Fehler zu hören
Um die Aufnahmen anschließend einordnen zu können, verknüpften die Forscher*innen die subjektive Hör- und Bewertungsexpertise von Schweißspezialist*innen vor Ort mit den objektiven Parametern zum jeweiligen Maschinenzustand und den Ergebnissen konventioneller Qualitätsprüfungen. »Damit haben wir die Grundlage für das Training der AKoS-KI geschaffen, die nun Schritt für Schritt lernt, generelle Auffälligkeiten im Schweißprozess zu erkennen und frühzeitig vor möglichen Qualitätsmängeln zu warnen«, erklärt Breitbarth.
Das allein reicht allerdings nicht. Denn Schweißgeräusch ist nicht gleich Schweißgeräusch und die jeweils verwendeten Verfahren und die jeweilige Anlage bieten unterschiedliche akustische Voraussetzungen. Die KI muss also zusätzlich noch auf den jeweiligen Anwendungsfall trainiert werden.
Ein erster Schwerpunkt des Projekts liegt deshalb auf dem Anwendungsfall »additive Fertigung mit Rührreibschweißen«. »Im Testlabor erzielt unsere KI dabei bereits Erkennungsquoten von etwa 90 Prozent«, sagt Breitbarth. Aktuell laufen dazu aber noch weitere Tests bei einem Industriepartner. Die Ergebnisse nutzen die Forscher*innen, um das System weiter zu verbessern. Danach sollen jeweils wenige Probedurchläufe genügen, um das Analysesystem auch auf anderen Anlagen einsetzen zu können.
Ein zweiter Schwerpunkt ist das Metall-Schutzgas-Schweißen (MSN). Das Verfahren wird häufig bei der Serienfertigung genutzt. Hier soll das System vor allem erkennen, wann die Schweißeinrichtungen erste Verschleißerscheinungen zeigen. »Arbeitet der Drahtvorschub beispielsweise nicht mehr vollständig korrekt, soll unser System dies so rechtzeitig heraushören, dass ein Werkzeugtausch vorgenommen werden kann, bevor es zu nicht mehr akzeptablen Qualitätsmängeln bei den Schweißergebnissen kommt«, so Breitbarth.
Pilotsystem verschlanken
Dass für das AKoS-System bis auf Weiteres noch der Messkoffer genutzt wird, ist durchaus gewollt: »Noch fehlen uns die Erfahrungen, um abschließend entscheiden zu können, mit welchem Technologie-Set wir je nach Anwendungsfall die beste Qualitätssicherung erreichen«, erklärt Breitbarth. Insofern sei ein flexibler Werkzeugkoffer die richtige Wahl. Im Moment setzen die Forscher*innen beispielsweise immer noch viele Mikrofone ein und überwachen das Vibrationsverhalten der Roboter und Automaten sowie die Zustandsparameter. Die so gewonnene breite Wissensbasis aber nutzen sie, um ihre Mess- und Analyseverfahren weiterzuentwickeln.
»Es zeichnet sich aber bereits heute ab, dass für viele Anwendungen ein System aus einem leicht anzubringenden Mikrofon plus der zugehörigen Analysesoftware tatsächlich ausreichen wird«, prognostiziert Breitbarth. Übergeordnetes Ziel aber seien generelle Erkenntnisse für eine verlässliche Qualitätssicherung. Um diese auch für Anwendungen zu ermöglichen, bei denen ein akustisches Monitoring allein nicht ausreicht, wollen die Projektpartner deshalb noch weitere System-Setups entwickeln.
(stw)
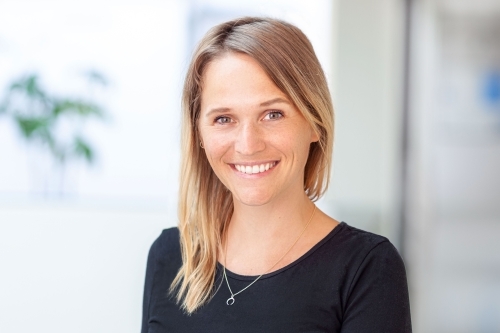
Expert*in
Kati Breitbarth
Fraunhofer-Institut für Digitale Medientechnologie IDMT