Highspeed-Fähren mit Elektroantrieb effizient entwickeln und bauen
Die Elektrifizierung der Mobilität und Logistik darf nicht am Ufer halt machen. Dafür wurde im Rahmen des Konsortialprojekts »TrAM«, an dem das Fraunhofer IEM mitwirkt, die erste elektrische Hochgeschwindigkeitsfähre der Welt entwickelt, die nun in den Fjorden von Norwegen verkehrt und als »Ship of the Year 2022« gekürt wurde. Durch den Einsatz von vor-zertifizierten Modulen können an örtliche Anforderungen angepasste Versionen der grünen Fähre deutlich schneller zu Wasser gelassen werden – volle Fahrt voraus für den emissionsfreien Personen- und Gütertransport auch auf Wasserwegen.
Mit dem »Green Deal« will die EU den vom Verkehr verursachten Treibhausgas-Ausstoß um 90 Prozent senken – inklusive der Schifffahrt. Um die Entwicklung klimaneutraler Antriebe voranzutreiben, müssen künftig auch Reedereien CO2-Emissionszertifikate kaufen – oder auf umweltfreundliche Schiffe umstellen. Elektrische Schnellfähren zum Beispiel. Allerdings gibt es solche bislang nicht. Und sie mit den bisherigen Methoden zu konstruieren und zu bauen braucht Zeit und (zu) viel Geld. Retten könnte die Schiffsindustrie ein EU-Projekt. Dank »TrAM«, so die Hoffnung, heißt es bald: Land in Sicht!
Dass eine Highspeed-Fähre mit 23 Knoten, also rund 40 Kilometern in der Stunde, ihre Passagier*innen vom norwegischen Stavanger zu den umliegenden Inseln bringt, ist beeindruckend, wäre im Grunde aber keiner Schlagzeile wert. Gäbe es nicht die »Medstraum«, die seit einigen Monaten diese Aufgabe übernimmt. Denn das Schiff ist die weltweit erste emissionsfreie Hochgeschwindigkeitsfähre. Für den Antrieb sorgen nicht mehr, wie seit hundert Jahren eigentlich üblich, Dieselaggregat und Kraftstofftank, sondern zwei Elektromotoren sowie ein Batteriesystem mit einer Kapazität von 1.500 Kilowattstunden und einer Ladeleistung von über zwei Megawatt. Dank des Stroms an Bord spart das Schiff in etwa den CO2-Ausstoß von 30 dieselbetriebenen Bussen ein.
Einzigartig ist die neue Fähre aber noch aus einem weiteren Grund. Sie ist die erste, bei deren Konstruktion und Bau neue, modulare Entwicklungs- und Produktionsmethoden genutzt wurden. Diese wiederrum sind – zusätzlich zum Bau des Schiffes selbst – Ergebnis der umfassenden, europaweit agierenden Forschungskooperation »TrAM – Transport: Advanced and Modular«: In diesem Projekt arbeiten vierzehn Partner aus Wissenschaft, maritimer Industrie und Fährlinienbetreibern seit 2018 intensiv zusammen. Die EU unterstützt das Vorhaben im Rahmen des Förderprogramms Horizon 2020.
Tobias Seidenberg vom beteiligten Fraunhofer-Institut für Entwurfstechnik Mechatronik IEM erklärt das Ziel: »Wir wollen die Elektromobilität zu Wasser bringen – und zwar auf höchstem Leistungsniveau. Dafür arbeiten im TrAM-Projekt renommierte Expert*innen aus allen Fachdomänen und Gewerken europaweit zusammen. Durch die gemeinsame Arbeit werden bis zu siebzig Prozent der Entwicklungszeiten eingespart und die Produktionskosten von Fähren um ein Viertel reduziert.« Und damit, so Seidenberg weiter, schaffen wir eine grundlegende Voraussetzung, um vollelektrische Hochgeschwindigkeitsfähren europaweit vor allem auf Wasserwegen in urbanem Umfeld einzusetzen und so eine emissionsfreie Personen- und Güterschifffahrt auch auf dem Wasser zu gewährleisten.
Schiffsbau neu gedacht
Wie nachhaltig wirkungsvoll dieser Ansatz sein kann, zeigt die Medstraum. Denn die 150 Personen-Fähre ist nicht nur einfach eine elektrifizierte Version ihrer dieselbetriebenen Kollegen. Sie ist ein komplett neu entwickelter Schiffstyp. »Diese Vorgehensweise war zwar aufwendig, ist aber auch notwendig«, sagt Seidenberg. »Um die hohen Fahrgeschwindigkeiten vollelektrisch zu erreichen, müssen nicht nur die Motoren und Batterien extrem leistungsfähig sein. Antrieb und Schiffsdesign müssen neu und als Einheit gedacht und konzipiert werden, um Leistung und Wirtschaftlichkeit gleichermaßen zu optimieren«, betont Seidenberg. Und das gelte sowohl in Bezug auf die eingesetzten Technologien als auch hinsichtlich der Anschaffungs- und Lebenszykluskosten sowie der Energieeffizienz. Um all das möglich zu machen, wurden für nahezu alle Bestandteile des Schiffes neue Richtlinien und Verfahren ausgearbeitet und präzisiert, diskutiert, optimiert, weiterverfolgt und umgesetzt.
Einige der ursprünglich vielversprechendsten Entwürfe mussten die Forscher*innen allerdings wieder über Bord werfen. Die Montage der Batterien ganz unten im Schiffsrumpf beispielsweise. Die Elektroingenieur*innen hatten eigentlich gute Argumente dafür. Umgeben vom Wasser ist die notwendige Kühlung der Akkus einfach. Und das tief liegende Gewicht wirkt sich zudem positiv auf die Gewichtsverteilung aus. Im Austausch mit den Spezialist*innen für Hydrodynamik, Rumpfdesign und Schiffsbetrieb zeigte sich jedoch: Die Batterien sollten besser auf dem Oberdeck montiert werden. Denn im Rumpf würden sie den Spielraum für die geplante, hydrostatisch optimierte Gestaltung erheblich einschränken. Zudem ist so gewährleistet, dass die Akkus und die Hochvoltelektrik problemlos und zügig gewartet werden können.
»Das aber ist nur ein Beispiel für eine Vielzahl an neuen Fragestellungen, die bei der Entwicklung der Medstraum grundlegend neu durchdacht und gelöst werden mussten«, sagt Seidenberg.
Dolmetscher zwischen den Fachdisziplinen
Trotz fehlender Benchmarks, auf die man sich dabei hätte stützen können, wollte das Projektteam im Vergleich zu den in der Regel eher trägen schiffsbauüblichen Entwicklungszeiten schnell zum Erfolg kommen. Die Verantwortlichen setzten deshalb auf das Model-Based Systems Engineering, einer Art »Enabler« für mehr Effizienz und Geschwindigkeit bei Entwurf und Umsetzung komplexer mechanisch-elektrischer Systeme. Der Vorteil dieses Systems: Die Expert*innen aller beteiligten Fachdomänen können von Beginn an mit einem gemeinsamen Modell arbeiten, das als »Dolmetscher« zwischen den Einzeldisziplinen fungiert – von Statik, Hydromechanik und Fertigungstechnik bis hin zu Elektrik und Informatik. Gleichzeitig ermöglicht der modellbasierte Ansatz, das zu entwickelnde Gesamtsystem zu modularisieren. Dadurch lassen sich die einzelnen Module getrennt voneinander und vor allem auch parallel spezifizieren und entwickeln. Über das Gesamtmodell sind dabei die Anforderungen sämtlicher Schnittstellen eines Moduls zu den anderen definiert. So bleibt gewährleistet, dass die einzelnen Teile ins Gesamtsystem passen. »Die Methode ist in vielen Branchen bewährt. Für ihre Anwendung im Schiffsbau aber mussten wir aber erst noch gemeinsam mit unseren Partnern das zugrunde liegende Systemverständnis erarbeiten, die Vorgehensweisen und Tools anpassen und die Plattformarchitektur für das Schiff entwickeln«, so Seidenberg.
Individualität in Serie
Trotz des Aufwands und der für die Passagiere mittlerweile täglich erfahrbaren elektrisch zurückgelegten Wegstrecken wird die Medstraum nicht als Duplikat in Serie gehen. »Das war auch nie unser Ziel und wäre wenig sinnvoll«, sagt Seidenberg. Sie Einsatzbedingungen und Anforderungen an Fährschiffe quer über Europa sind dafür schlicht zu unterschiedlich. So muss etwa die Medstraum vor der Küste Norwegens auch schwerer See trotzen können. Bei einer Highspeedfähre, die öffentlichen Nahverkehr entlang der (deutlich ruhigeren) Themse in London bieten soll, haben dagegen niedriger Tiefgang, Platz für mehr Personen als die 150, die die Medstraum aufnehmen kann, und kurze Anlegezeiten oberste Priorität. Das ist auch der Grund, warum Schnellfähren bisher weitgehend individuell entworfene Einzelanfertigungen sind. »Auch mit der TrAM-Methodik werden Fähren künftig individuell so angepasst werden können, dass sie auf die jeweiligen Bedingungen und den Einsatzzweck spezialisiert sind«, sagt Seidenberg.
Trotzdem aber sollen und werden die Werften und ihre Auftraggeber die Zeit- und Kostenvorteile einer Fertigung in größeren Stückzahlen nutzen können. Die Entwicklungsplattform der Projektpartner ist darauf ausgelegt. Denn Entwurf und Bau einer neuen Hochgeschwindigkeitsfähre nutzen ein Baukastenprinzip: Die einzelnen Module lassen sich dann flexibel je nach Anforderung neu zusammenstellen und je nach Bedarf um weitere neue Elemente ergänzen. Neu entwickelt werden müssen also nurmehr die Teile des Schiffes, die in der Form, wie sie gebraucht werden noch nicht im Baukasten vorhanden sind.
Der Vorsprung, der sich aus dieser Vorgehensweise ergibt, ist enorm, meint Seidenberg. Nicht nur, weil viele der Module in Serie gefertigt werden können, um sie dann je nach Bedarf für den spezifischen Bau einer Fähre zu nutzen. Sondern auch, weil die Wiederverwendung einzelner Module die behördlichen Zertifizierungsprozesse beschleunigt. »Gerade im Bereich der Hochgeschwindigkeitsfähren sind umfangreiche Berechnungen, Tests und Zertifizierungen Pflicht – von technischer Sicherheit und Zuverlässigkeit über Brandschutzauflagen bis zum umfassenden Schutz von Besatzung und Passagier*innen«, erklärt Seidenberg. Mit der TrAM-Methode sind einzelne Module bereits mit anderen Schiffen zertifiziert worden, wodurch die Abnahme des neuen Schiffs entsprechend einfacher und schneller vonstattengehen kann.
Nachhaltig und Update-fähig
Die konsequente Modularisierung beschleunigt und vereinfacht aber nicht nur die Entwicklung und den Bau der Schiffe. Sie sorgt auch dafür, dass die Fähren erheblich flexibler, wirtschaftlicher und nachhaltiger betrieben werden können. Verändern sich zum Beispiel die Anforderungen an ein Schiff, lässt es sich durch den Austausch einzelner Module leichter anpassen. Beispielsweise, um an Deck zusätzliches Frachtgut transportieren zu können. Ähnliches gilt für die Wartung: »Flottenbetreiber können Module mit einem höheren Verschleiß- oder Ausfallrisiko sogar zum Austausch vorhalten und so kostspielige Standzeiten vermeiden«, so Seidenberg. Und auch das aktuelle Batteriesystem lässt sich schneller durch ein leistungsstärkeres ersetzen: »Gerade bei den Batterien ist die technische Entwicklung derzeit äußerst dynamisch. Es ist also durchaus möglich, dass es in wenigen Jahren neuartige Akkupacks mit erheblich weniger Gewicht und höherer Leistung gibt, so dass ein kompletter Austausch des Energiemoduls auch aus wirtschaftlicher Sicht sinnvoll ist«, so Seidenberg. Vergleichbares gelte auch für neue Steuerungssysteme wie beispielsweise autonome Fahrassistenten oder eine effizientere Hochvoltenergietechnik.
Vom ersten Schiff zu vielen
Für TrAM ist die Medstraum schon heute ein konkreter und nachhaltiger Erfolg. Denn sie leistet nicht nur zuverlässig seine Fährdienste, sie ist gleichzeitig auch ein schwimmender Demonstrator, mit dem die Projektpartner zum einen bewiesen haben, dass die Hochgeschwindigkeits-Schifffahrt auch vollelektrisch möglich ist und dass die modellbasierte Entwicklung in Modulbauweise funktioniert. Fast folgerichtig ist es, dass die Medstraum auf der Weltleitmesse für maritime Wirtschaft SMM in Hamburg zum »Ship of the Year 2022« gekürt wurde.
Ganz an ihrem Ziel sind die Projektpartner damit allerdings noch nicht. Was sie noch ausarbeiten wollen sind Umsetzungsanalysen für weitere Schiffe, um eine sinnvolle Anwendung ihres Modulbaukastens auch für andersartige Fähren nachzuweisen: Beispielsweise bei einer Highspeedfähre für den Linieneinsatz entlang der Themse in London beim Projektpartner »Uber boat by Thames Clippers« und bei einer elektrifizierten Fähre, die optimal auf die Bedingungen der Schifffahrt des Partners »De Vlaamse Waterveg« auf den Inlandskanälen im belgischen Flandern vorbereitet ist.
(stw)
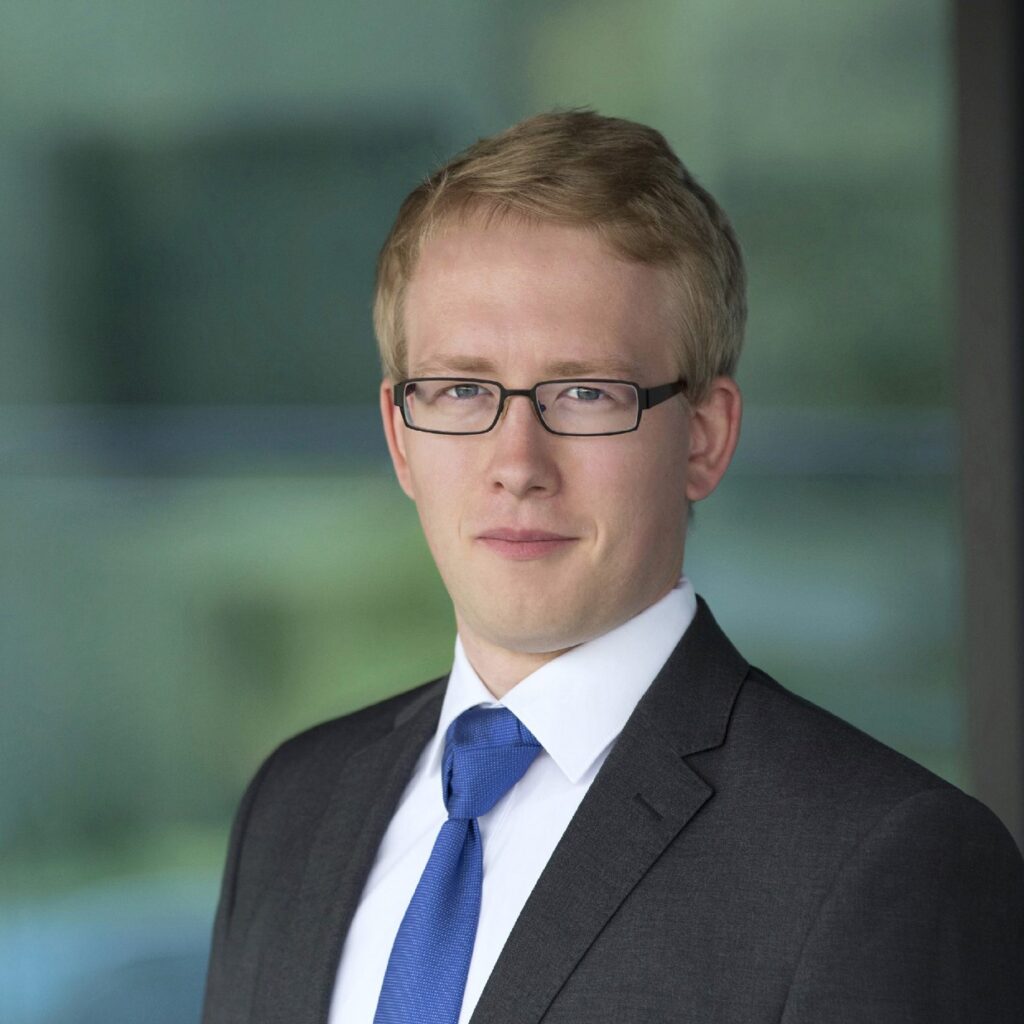
Expert*in
Tobias Seidenberg
Fraunhofer-Institut für Entwurfstechnik Mechatronik IEM